Advancements in Hydrostatic Test System Design

Shawn Glover, VP of Sales, Dec 6, 2024
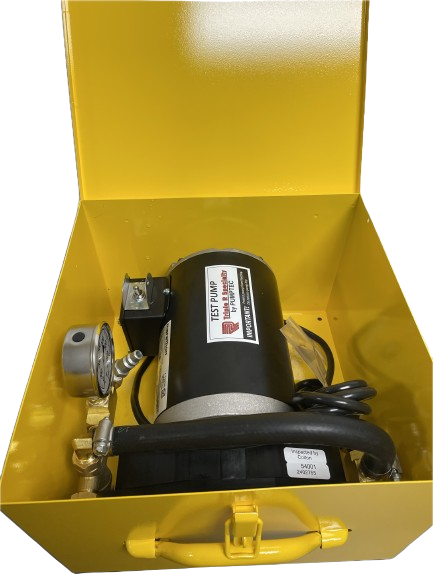
The idea of using pressurized water to test the integrity of pipes and pressure vessels has been around for centuries. As with all technology, hydrostatic test systems have enjoyed several advancements since the days of the Roman aqueducts. Today, hydrostatic testing is a vital process used to ensure pressure vessels and piping systems are capable of withstanding operating conditions. In some places and industries, hydrostatic pressure testing of critical systems is mandatory, with certified inspectors testing multiple buildings a day. Recent advances in hydrostatic test pump design are geared towards extending the life of the pump while reducing test time.
Innovations in Hydrostatic Test System Design
When it comes to recent advancements in hydrostatic testing, the main advantages come from innovative design features for key components that not only enhance efficiency but also enable easier and quicker operation.
Protective Case
System inspection is a rough job, taking inspectors to construction sites and other harsh environments. After hauling their test pump around all day, inspectors aren’t known for gentle equipment handling, inadvertently causing damages. Pumptec’s solution is a lightweight case that protects the pump from debris and impact damage.
Pump Style
Consistent pressure is critical for accurate pressure testing. Inspectors look for fluctuating pressure readings as well as water leaks to help determine if a system is performing as required. As a result, pumps used for hydrostatic testing cannot experience an ebb and flow in pressure, such as occurs in diaphragm-style pumps. Plunger pumps, on the other hand, maintain consistent pressure during operation.
Pressure Regulator
As previously mentioned, consistent pressure must be maintained for accurate results. Pressure regulators are one of the key components that ensure consistent pressure. If the system overpressurizes, the regulator bypasses the flow, preventing seal failure or system rupture.
Seal Packages
Advancements in seal design and manufacturing allow for more precision fitting and longer durability during prolonged operation. This is particularly important when you consider the daily use system inspectors put their testing systems through. With more reliable seals, inspectors don’t have to worry about unexpected downtime for pump maintenance.
Lightweight Construction
Hauling a hydrostatic test system up dozens of flights of steps multiple times a day takes a major toll on the body. Innovations in material science have produced high-quality durable alloys with greater strength-to-weight ratios, effectively allowing the production of reliable hydrostatic pumps at a fraction of the weight of older systems.
Liquid-Filled Gauges
Even with design adjustments to compensate for operational vibrations, a hydrostatic test system will still produce enough vibrations to interfere with gauge operation. Liquid-filled gauges dampen the vibrations, allowing for more precise readings.
Looking to the Future of Hydrostatic Pressure Testing
Technology has a tendency to advance at dizzying speeds, with the newest innovation just around the corner. Here at Pumptec, we’re always looking for ways to improve and enhance our pumps to better meet the needs of our distributors and their customers.
Contact us today to learn more about our advanced hydrostatic test systems.