What is Cavitation in Pumps? Learn the Causes and Cures

Shawn Glover, VP of Sales, Aug 31, 2021
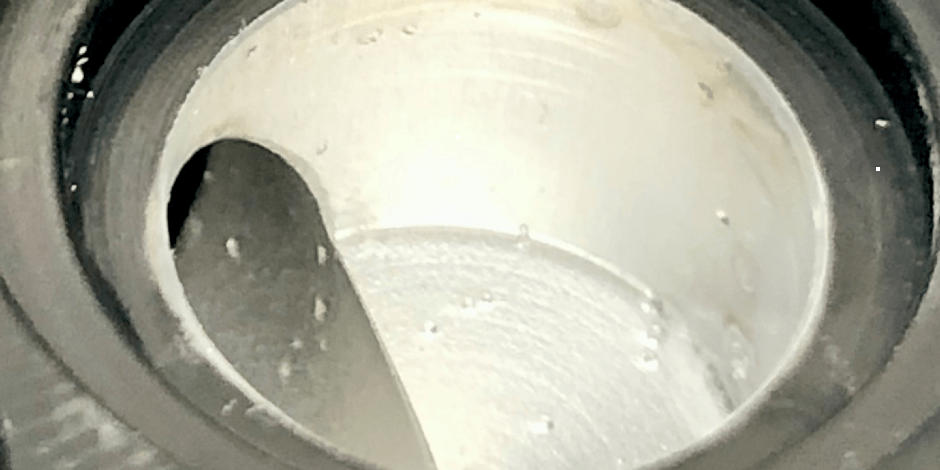
Pumps are designed to produce enough flow and pressure to move a liquid from one location to the next. Sounds simple enough, but the internal system of a pump is complex. When you combine the complexity of the pump system with the wide-ranging properties of various fluids, the surrounding environment, and other factors, cavitation can occur.
Pump cavitation is a potentially damaging problem in pumps that are not properly configured or being used for their intended application. Here, we’ll explore what causes cavitation in pumps, the signs to look for, and ways to prevent it from happening.
What is Cavitation in Pumps?
Pumps are designed to pump liquids but, when the combined flow rate and pressure are inadequate or not conducive to the type of liquid being pumped, pockets or cavities can form, resulting in cavitation.
Some describe pump cavitation as the creation and collapse of the air bubbles in a fluid. While they may appear to look like air, those bubbles are technically a cavity, gaseous vapor, or vacuum. While cavitation is possible in all pump types, it is more common in centrifugal pumps where the bubbles quickly develop around the impeller’s axis. When the bubbles pass from the middle of the impeller to the outer edges, the centrifugal force creates higher pressure, causing those bubbles to quickly collapse or implode with great force.
Pump cavitation is the rapid succession and released energy of the implosions of gaseous cavities which cause an intense rattling sensation that can damage a pump.
Common Causes of Pump Cavitation
Various conditions can make a pump more prone to cavitation. A clogged filter or strainer, for example, can easily restrict flow and lead to pump cavitation. Similarly, a restricted or flimsy inlet hose might collapse and cause issues. Fluid viscosity is a major contributor, too, especially when combined with the wrong hose. Imagine drinking a milkshake through a thin straw: the combination of the thick viscosity, pressure, and weak structure of the straw causes it to collapse and restricts the flow. Or consider if that straw has a pinhole in it; the leak would also affect flow and pressure. Similar phenomena can occur in pump systems.
That said, the inlet supply hose can’t be too rigid either. If you use a solid metal hose or a system is plumbed with hard PVC or copper piping, it could cause water hammering. Finding the right combination of dampening with a strong yet soft inlet hose or flexible PVC is ideal. Here at Pumptec, we use pulse hoses with metal springs inside them to add strength and rigidity. They’re less likely to collapse yet still offer the right level of flexibility.
The position of the reservoir tank also makes a difference. If the tank is positioned below the pump, the pump will need to decrease pressure to draw the fluid vertically through the inlet piping. The longer the inlet hose and the farther the vertical distance between the tank and the pump, the greater the chance of creating a vacuum and cavitation.
Heated liquids are a major contributor to cavitation, too, especially as the hot fluid approaches the boiling point and creates additional vapor pressure. In this instance, the liquid needs to be fed/pushed through a pump rather than drawn/pulled through it. The easiest way to achieve this is to have the tank containing the heated fluid elevated above the pump so that it is gravity fed into the pump system.
In all these instances, the flow is being disrupted or poorly executed, causing the discharge pressure to fall. The pump is basically being starved of fluid, resulting in cavitation.
What are Signs of Cavitation in Pumps?
Obvious signs of pump cavitation are excessive noise and vibration. The implosions and released energy within the system produce a loud growling sound, or it may sound and feel like gravel is circulating through the system.
The most concerning signs of cavitation, however, occur internally and may not be apparent without dismantling the system.
Cavitation can damage seals, O-rings, and bearings, resulting in leaks and loss of pressure. On a centrifugal pump, the constant force of the implosions can erode the impeller and pump housing. Because of the added strain, the pump will also consume more power than it should.
On a positive displacement plunger pump, cavitation can erode seals and the metal around the poppet and seat on the check valves. If the pump body is made of anodized aluminum, which appears as a black coating, the black anodization will wear away upstream from the outlet check valve. In extreme cases, wear will occur outside of the main seal. If that happens, the pump will start sucking air, and bubbles — sometimes called washout — will form on the outlet.
Left unchecked, cavitation will eventually erode components beyond repair and lead to pump failure.
How to Prevent Pump Cavitation
Many of these issues can be prevented with proper maintenance and by selecting a pump that is designed for the intended use, accommodates the viscosity of the fluid being pumped, and has the proper configuration.
Some people think they just need to increase the size of the inlet hose. While it’s true that a hose that’s too small could cause cavitation, having a hose that’s too large could cause priming problems.
Centrifugal pumps have such high flow rates that it’s difficult to control their output, plus they have a lot of back pressure downstream that affects the amount of flow. Because of their lower flow rates, plunger pumps typically have fewer cavitation issues.
Additional tips to reduce cavitation in pumps:
- Use an adequate supply of liquid
- Use an inlet hose that is the recommended diameter
- Use as short of an inlet hose as possible
- Elevate the tank reservoir above the pump so it’s fed by gravity, creating a flooded inlet
- Make sure there aren’t restrictions in the inlet (too small of a hose, improper fittings, too many elbows, etc.)
- Ensure that filters are large enough and are not plugged — inspect regularly
- Use flexible inlet hoses that contain internal springs to prevent hose collapsing while absorbing water hammer
All in all, the pump pressure must be maintained above the liquid's vapor pressure to avoid cavitation. In the end, the best tip for reducing cavitation is to work with a pump manufacturer to determine the proper use and placement for your application.
Contact the pump experts at Pumptec to discuss your pump challenges and how to overcome them with a solution that’s customized to your application. Get a head start by checking out our Guide to Proper Pump GPM and PSI below.