The Difference Between Volts and Amps and Why it Matters

Shawn Glover, VP of Sales, May 3, 2022
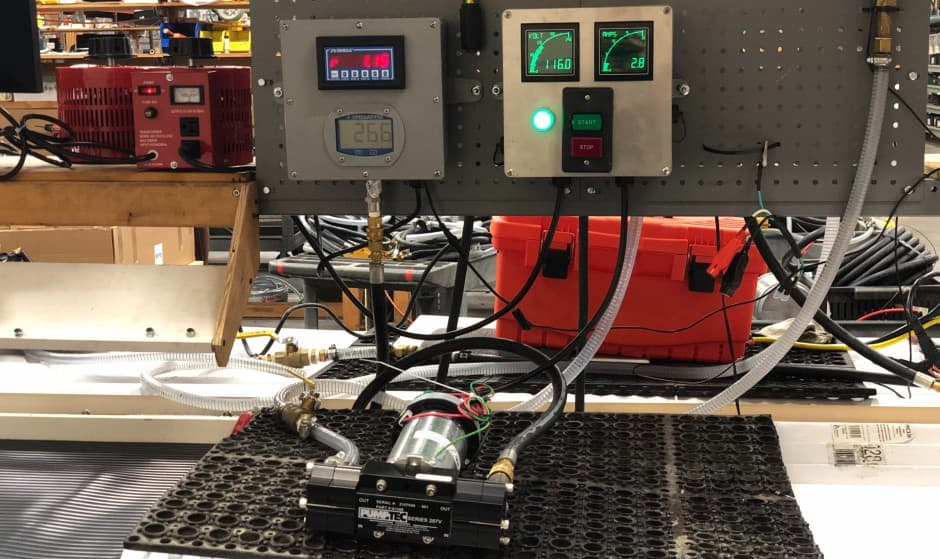
Numerous factors affect a high pressure plunger pump’s performance, from its design and materials to its flow and pressure. Ultimately, however, it's the motor’s ability to produce and sustain the right amount of power that makes a pump operate properly.
Knowing how many amps and volts a pump motor produces is a key consideration when determining which pump model is right for an application. You don’t need to be an electrical engineer to understand the difference between volts and amps. We’ll break down these measures of electricity and help you understand how to use that knowledge to your advantage when selecting a pump model.
What are Volts?
Volts, or voltage, are units of measurement showing the force, or how strongly electrons are pushed through a wire or electrical cable.
Volt Analogy: Just like pressure forces fluid through a pump hose, voltage pushes electricity through a wire.
What are Amps?
Amps, sometimes called ampere or amperage, are units of measurement showing the rate — or how fast — electrons flow through an electrical wire.
Amp Analogy: Similarly to how a fluid’s flow rate through a pump’s hose can be measured in gallons per minute (GPM), an electrical current’s flow through a circuit is measured in amps.
What are Watts?
Watts are a combination of voltage and amp currents and represent the total amount of electricity that will go through a system.
Watts Analogy: Just like a pump’s horsepower is determined by its flow and pressure (Flow x Pressure = HP), watts are determined by calculating the volts and amps (Volts x Amps = Watts).
Real-Life Application
Do I Need Higher Voltage or Higher Amperage?
Understanding the relationship between volts and amps is important, but how do you translate that knowledge into a practical application? Let’s use a soft wash pump as an example to help you determine how to choose the proper motor ratings for a pump system.
RELATED: Soft Wash Pump System Case Study
Say you have a soft wash system with a 12V motor that is rated at 30 amps. You likely chose the 12V motor because your truck’s battery runs on 12V. At 30 amps, however, you’re likely pushing the limits and even going beyond 30 amps when trying to get more pressure out of your pump to get greater vertical and horizontal throw. When that happens, you’ll notice the motor overheating and it may even start to emit smoke or a burning smell. Obviously, doing this over time will ruin the pump motor.
You could reduce the load and amps by reducing the pressure with a bigger nozzle, but you’d also be reducing performance and how far your stream of cleaning solution will shoot. If you need performance, and changing pressure isn’t an option, then you need a more powerful motor. There are two potential solutions:
Option One: Use a pump rated at higher voltage
You could go to a higher voltage motor like a 24V motor and stick with 30 amps (it will be double the power because you doubled the voltage). However, if you use a 24V motor, you’ll have to think about how to power it. Most mobile units run off a 12V truck battery. To double the voltage will require the addition of another 12V battery.
Option Two: Use a pump rated at higher amperage
Instead of doubling the volts, a better solution might be to double the amperage. You can stick with a 12V motor, but select one that’s rated at 60–70 amps to achieve the power you need to get the job done. You may need to add battery capacity and check the charging system and/or your truck's charging system.
Pump Motor Volt and Amp Recommendations
So, what is the difference between volts and amps and how do you determine how much power you need for a high-pressure pump application?
A higher flow rate requires a bigger motor, but so does higher pressure. They impact the electrical load equally.
For example, the recommended flow and pressure for the aforementioned soft wash application is 6 GPM and 150 PSI. Our XPVC pump series can produce these results and draws 60–70 amps on a 12V motor.
A misting system, on the other hand, requires much higher pressure to produce fine droplets, but significantly less flow. Our 113C misting pump produces .25 GPM at 800–1000 PSI, but it only draws 15 amps so it can use a much smaller motor. The motor is smaller because even though the PSI is more than five times higher, the GPM is 24 times less than the soft wash pump.
To recap, if your pump application requires low flow and high pressure, you will often draw fewer amps and can use a smaller motor. If your pump application requires high flow rates at low pressure, you will often draw more amps and need a larger motor.
Determining how much power you need for an application is critical, and we realize that this simple overview of volts and amps may only touch the surface. To further help determine your pump needs, check out our helpful Guide for Proper Pump GPM and PSI.
Our team of pump engineers have the knowledge and experience to pinpoint your needs, including power, pressure, flow, materials, and much more. Contact them today to talk through your pump challenges and get the performance and durability you deserve.