Pump Noise Levels and Causes: What You Need to Know

Shawn Glover, VP of Sales, Sep 28, 2021
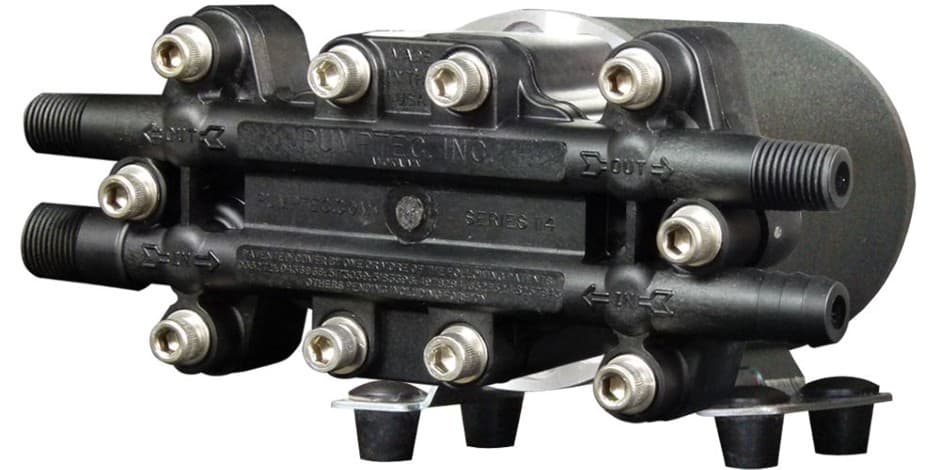
Commercial high pressure pumps used for agricultural, commercial cleaning, pest control, and other industries have a lot of moving parts. Those parts inevitably make some noise.
Some plunger pump noise is acceptable, but there are times when high noise levels indicate that something is wrong. Noises that begin suddenly or increase in volume over time might indicate one of the following problems and be a sign that it’s time to do some critical pump maintenance to achieve pump noise reduction.
Problems and Noisy Pump Causes
1. Cavitation or Water Hammering
A rattling sound inside a pump may be caused by damaging cavitation, resulting from imploding internal gaseous bubbles due to restricted flow, improper pressure, or other issues. Likewise, water hammering, a single implosion of a large gaseous bubble or air pocket might sound like a loud bang. Take steps to eliminate cavitation.
2. Worn Seals and Leaking Inlet Plumbing
If a pump’s seals are going bad, cracked, or dried out, they can form leaks. Air leaks in inlet plumbing can create very loud noises. Similarly to cavitation, it can ruin a pump if not corrected. Check all the connections regularly to verify a proper seal.
3. Poor Inlet Plumbing Configurations
If you have a big plastic housing that has a built-in tank, or hoses that run loosely along the floor of the plastic housing and you place a pump on top of it, it will likely result in excessive noise. Likewise, any hose that’s not routed in a way that keeps it away from the walls and housing could cause issues.
4. Worn Cam Bearing
If a pump is nearing the end of its life, the plunger slot and cam bearing that’s attached to the end of the motor can wear out. Proper maintenance can help avoid this issue.
5. Contaminated Grease or Oil
Particulates in the lubricant could scratch and damage a pump system, resulting in noise. A lack of preventative maintenance or a dirty environment can cause issues and even lead to a loss of lubricating grease. Water contamination could cause connecting rods to open up. The pump will knock like a car engine, especially with the change of speed/load and the starting and stopping of the motor.
6. Low Oil
Many pumps use an oil bath that will drain out if the pump is not kept upright. The resulting low oil levels will cause the pump to wear out and could even cause the connecting rod to blow out the top of the pump. Pumptec pumps do not use an oil bath and can run in any orientation and be stored on their sides, so no worries.
7. Loose Plunger Slot
If a plunger slot is loose, each time the cam goes around it will impact the plunger more, causing noise.
8. Pump Drive Problem
A slapping sound may indicate a problem with the pump drive or power supply.
9. Improper Outlet Hose
Pulsation can occur in hoses that are too weak, too long, too rigid, or too soft, causing a drumming sound. Using a pulse hose can help to minimize pulsations due to its ability to dissipate energy and built-up pressure, smoothing the flow of liquids.
10. Improperly Secured Equipment
If a pump isn’t properly secured to the equipment, it can cause components to rattle or bang around. Use rubber vibration isolation mounts to dampen the impact and make sure all fittings are tightened.
11. Plugged or Worn Check Valve
If you have a check valve that’s plugged or worn out, you can lose flow from one head of the pump, cutting flow in half. In this case, only one side of the pump is working and will cause a noticeable pulsation.
12. High Flow
While not a problem, high flow — especially at low pressure — is more prone to noise and should be expected at some level. As you go up in performance, especially flow, you’ll get more noise. Higher flow rate pumps have larger plungers with more movement because the cam is offset farther than with smaller pumps, creating more vibration and noise.
In most cases, pump problems that lead to excessive noise can be avoided with proper maintenance.
What Pump Noise Level is Acceptable?
What if you feel like the pump is too noisy right out of the box? The type of pump and the desired performance will help inform what an acceptable decibel level should be. An electric or battery-powered pump should have a consistent hum and will generally operate around 80-85 dB or lower. Some gas-powered pumps can be over 100 dB due to their internal combustion engines, requiring hearing protection. The benefits of electric vs. gas-powered pump noise levels are easy to see.
A centrifugal pump is typically the quietest because it doesn’t have parts changing direction; it mostly has a fan that spins. But it’s also the least efficient, requiring four times as much horsepower as a plunger pump to achieve the same GPM and PSI.
Diaphragm pumps are also quiet because valves are usually made of rubber. However, to achieve high pressure that compares with plunger pumps, valves need to be manufactured out of rigid materials like stainless steel which produce a mechanical noise.
Plunger pumps may have a slightly higher noise level than standard centrifugal or diaphragm pumps, but are often much more suited to commercial uses that require long-lasting durability and precise flow and coverage.
But the hard truth is that it’s difficult to pinpoint acceptable pump noise levels due to the subjective nature of defining noise. The location or setting where a pump is operated might inform someone’s opinion of whether a pump is too noisy. For example, a certain decibel level might be acceptable in an agricultural setting, but seem too loud in a residential neighborhood.
How Are Decibel Ratings Measured?
The standard decibel rating that is published in product manuals requires laborious tests under highly controlled environments and conditions. Sometimes these official tests take place in soundproof booths, require calibrated microphones and equipment, or are a result of multiple samples taken from several directions, distances, and heights that are all averaged together.
The problem is that an operator with a decibel reader app on their iPhone isn’t following those rules or operating their pump in such a controlled environment. They might hold their phone a foot away from the pump on the back of their pickup truck and be frustrated that it exceeds the stated rating that was taken at a 3-meter distance in a soundproof booth. Their meter reading will inevitably be inconsistent with those published in the owner's manual, but it may, in fact, be operating exactly according to specifications.
Pumps also come in different models and may be rated at specific performance levels using certain nozzles. There’s no guarantee that the operator will run it at the same performance level or with the same accessories.
As you can see, decibel ratings are sometimes a moving target. Unless your pump is experiencing some of the problems noted earlier, your pump may be operating exactly as designed.
Of course, you could choose a pump model rated at lower decibel levels, but there are trade offs to consider. Will reducing pump noise inevitably lead to reduced power, flow, and overall performance? Are there pumps that deliver quieter operation but fail to hold up over time?
In general, the harder the pump is working, the louder it will be.
It’s important to consider all the factors when gauging noise levels, including desired GPM and PSI. For more information on industry standards for pump GPM and PSI, be sure to check out our free guide below.
A small amount of noise may be acceptable if you’re getting the power, flow, and performance you need. At Pumptec, our pumps are sought after for their quiet yet powerful performance. If you have questions about pump noise levels or want to explore replacing your current pump systems, contact our pump experts today.