Choosing Chemical Resistant Pumps for Commercial Industries

Shawn Glover, VP of Sales, Nov 29, 2022
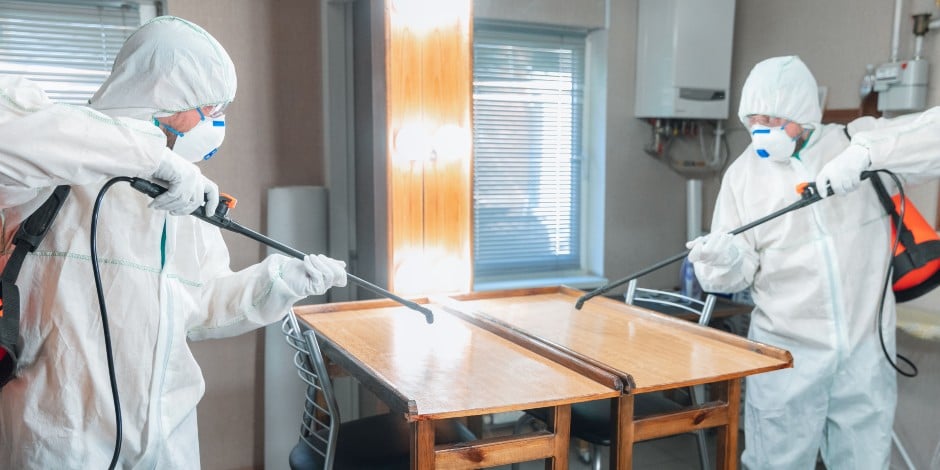
What’s one of the biggest drivers of pump failure? Chemical incompatibility.
While GPM and PSI are critical aspects of a pump’s performance, knowing which fluids come in contact with various components is the foundation of finding the right pump solution.
The types of chemicals that flow through pump systems are as varied as the industries in which they’re used. Ensuring chemical-resistant pump components and materials not only improves the longevity of the pump, it also helps ensure compliance with EPA standards and other regulations.
View our recommendations for common chemicals below, along with additional considerations when choosing a pump system for commercial applications.
Commercial-Grade Sodium Hypochlorite (Bleach)
Numerous industries use commercial-grade bleach to remove stains and mold, and to disinfect surfaces. Another form of bleach includes chlorine dioxide. Likewise, many surfactants are used in various applications, including soft wash, commercial cleaning, and disinfectant spray pumps.
- Pump Material: The pump housing should be engineered primarily out of PVC thermoplastic. It carries an A rating for sodium hypochlorite. Alloy C-276, a highly corrosion-resistant metal alloy, should be used for the valve body.
- Seals: Viton® O-rings
- Plunger: Ceramic
RELATED ARTICLES:
Pyrethrins, Pyrethroids and Fipronil
These chemicals are used widely in the pest control industry. Pyrethrins and pyrethroids are generally considered safe for pets and humans, but can harm aquatic life. Fipronil may be toxic to humans and animals. Minimizing overspray and runoff of any pesticide is critically important to help maintain safe operations and a balanced ecosystem.
- Pump Material: Pest control pumps are most often crafted out of aircraft-grade anodized aluminum with stainless steel valves.
- Seals: Viton® O-rings
- Plunger: Ceramic
Fertilizers and Herbicides
Numerous liquid fertilizers and herbicides are used in lawn care and agriculture, including nitrogen, phosphorus, potassium, glyphosate, dimethylamine salts, and other compounds.
- Pump Material: Agricultural and lawn care pumps are typically crafted out of aircraft-grade anodized aluminum with stainless steel valves.
- Seals: Viton® O-rings
- Plunger: Ceramic
Sodium Chloride (Salt)
While often not thought of as a chemical because it occurs naturally, seawater consists mostly of common salt, with some concentrations of magnesium chloride and calcium chloride. A desalination pump or reverse osmosis pump is used to make the water potable.
- Pump Material: Stainless steel is typically used for both the pump and valves in desalination applications.
- Seals: Viton® or Buna® O-rings
- Plunger: Ceramic
Other Chemical Compounds
Often, it’s not a single chemical that needs to be solved for. There may be multiple chemicals mixed together or used at varying stages of a pumping process. Such is the case with car washes that use foams, waxes, and various rinse cycles. These types of pump systems often have multiple chemical injection points, each pumping a different compound.
It’s critical to understand which combination of chemicals and at which concentration they are being used. Chemical compatibility charts are typically available from the chemical manufacturer and can help designate proper material selection. Be cautious referencing third-party compatibility charts as they are often incomplete and unreliable.
Preventing Pump Failure Due to Corrosive Chemicals
Improper pump selection and maintenance can lead to corrosion and pump failure from harsh chemicals and repeated use. Other issues like inconsistent flow or inadequate PSI to dispense recommended application rates by the manufacturer can also occur. To ensure optimal performance from your chemical-resistant pump system, follow these guidelines.
Proper Pump Material Selection
The materials used to construct a pump are what determine chemical compatibility.
RELATED: Selection Guide to High-Pressure Pump Body Materials
Corrosion, specifically, is only an issue that occurs with metal parts. Aluminum and stainless steel are typically the most reliable for use in commercial pump sprayers. For aluminum components, it’s important to ensure they’re protected by a layer of aluminum oxide which results from the anodizing process. Stainless steel is inherently corrosion-resistant unless exposed to chlorides or acids.
As for the plungers, the most likely material will be ceramic due to its inherent chemical compatibility and durability, although stainless steel may also be a consideration. Again, consult the chemical manufacturer and work closely with the pump manufacturer to be sure.
Despite being one of the smallest and least expensive components of a pump, the o-rings and seals are possibly the most vulnerable to chemicals.
When a plastic or elastomer and a chemical aren’t compatible, the compound will essentially attack it and cause the structure to break down, making it more likely to crack or rupture. Some chemicals can actually absorb into the material and cause the part to become soft or brittle, fluctuate in weight, and even change in dimension. Any of these issues can lead to lost pressure, poor flow rates and, ultimately, pump failure.
RELATED ARTICLE: Buna vs. Viton Elastomers and O-Rings
In a best-case scenario, you’ll find a manufacturer like Pumptec that can configure their pumps with a combination of materials and components specifically designed to withstand the harsh chemicals you specify.
Proper Pump Maintenance
Let’s not forget the importance of proper maintenance:
- After dispensing liquids, any pump should be flushed with clean water until the unit runs clear. Chemicals left inside the pump can corrode and damage internal parts resulting in rapid wear. Some chemical manufacturers recommend the use of a neutralizer in addition to flushing out the system with water. If the tank is stored empty, be sure to rinse it again prior to use to remove any residue.
- Check filters to ensure they’re properly installed, are compatible for the fluids being used, and aren’t plugged, and make sure the hoses you use are right-sized for the unit.
- Inspect the spray nozzle for damage or corrosion. These conditions not only restrict fluid flow, they can potentially cause cavitation damage. Remember to also clean the outside of the pump sprayer to remove any exterior chemical residue on the tank, nozzles, spray wand, and other components.
Pumptec plunger pumps provide even, consistent flow and can withstand higher PSI ratings than other types of pumps. When the reliable performance of a plunger pump is combined with the right materials and proper maintenance, you can expect your spray equipment to last for years, not weeks or months.
Access our helpful pump material selection guide below to provide further insights on durability, chemical compatibility, maximum PSI ratings, industry applications, and more.
Then, see how a custom pump solution that’s made with materials and engineering specifically designed for your application can save you time, frustration, and money. More importantly, it can help you ensure the safety of those around you. Contact a pump expert today.