What to Look for in a Dust Suppression Pump

Shawn Glover, VP of Sales, Apr 27, 2021
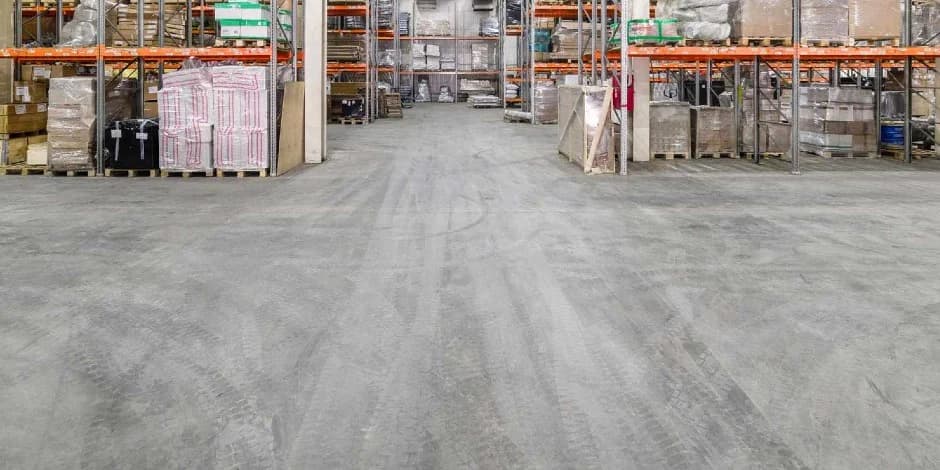
Dust suppression in construction, food processing, material handling, manufacturing, and other industries is necessary for reasons other than simply creating a more pleasant work environment and protecting electronics, machinery, and equipment. Workers exposed to fine dust particles can experience potentially life-threatening medical issues, including lung irritation, asthma, and disease.
In the building construction industry, in particular, dust suppression pumps help minimize crystalline silica particles that result from grinding, drilling, or cutting masonry materials like concrete, stone, brick, and mortar. Those who breathe these fine respirable particles are at risk of developing a deadly lung disease called Silicosis. The concern is so serious that Occupational Safety and Health Administration (OSHA) construction standards have been issued to control dust emissions.
Ensuring your dust suppression equipment operates properly and reliably is critical. To get the job done right, consider the following factors when choosing a high pressure pump for dust suppression.
OSHA Compliance
When it comes down to it, maintaining acceptable levels of particulates in the air is the ultimate goal. Some high pressure dust suppression systems use a HEPA vacuum system in an attempt to capture airborne dust particles. However, HEPA systems often fail to reduce levels below 50 micrograms of respirable silica crystalline dust per cubic meter when grinding stone products — the standard set by OSHA.
OSHA recommends a water-based dust suppression fog system to mitigate dust. Even some misting systems fail to meet these standards, however, so be sure tests are conducted to ensure compliance before deciding on a pump.
Proper Flow and Pressure
The goal of any dust control system is to provide just the right amount of mist to suppress dangerous particles without leaving a slippery, wet surface, exchanging one hazard for another. An important factor in obtaining a desired GPM and PSI is choosing the right nozzle size for an application.
One company developed a spraying system that could be adjusted precisely between 50 – 1,000 PSI and included four .006 nozzles around the base of the unit that created a “dust curtain.” The precise balance of PSI and nozzle size produced perfectly sized droplets to encapsulate dust particles and prevent them from becoming airborne.
View the Case Study: Concrete Grinding Tool Manufacturer Dust Curtain
Consistent Flow
While some high pressure water pumps may be spec’d out to produce specific flow rates, that doesn’t necessarily mean that the flow is always consistent. Some misting pumps tend to lose pressure or have a burst of fluid when turned off and on — a result of pressure that hasn’t been properly displaced — leaving a messy sludge. Some types of pumps have flexible components or designs that are inherently more prone to losing flow than others, such as diaphragm, centrifugal, or roller pumps.
A pressure regulator can help, but can only do so much when configured into an already inferior pump. To ensure consistent flow, choose a positive displacement pump, such as a piston or plunger pump. They have rigid components that can help ensure stable, fixed flow rates for a variety of applications.
Pump Comparison Chart: Pros & Cons of 7 Different Kinds of Pumps
Durability
It’s not unusual for dust suppression equipment to be housed in harsh environmental conditions. In construction, not only does a dust suppression system need to be compact enough to easily move from one construction site to the next, it needs to stand up to being hauled in and out of the back of a pickup truck. Suppression systems in manufacturing settings also need to be durable, able to withstand continuous vibrations from surrounding machinery.
For the most durable pump, choose one that’s crafted out of materials that can hold up to a little jostling here and there, such as aircraft-grade anodized aluminum. Not only does it have greater tensile strength than other metals, it’s also more resistant to corrosion and wear and tear.
Also consider whether you need tighter tolerances to achieve your goals, and whether the pump manufacturer’s accessories are compatible and durable enough to meet your standards. Some examples might include Buna or Viton o-rings, pulse hoses, controllers, regulators, and filters.
The engineers at Pumptec have worked closely with dust suppression equipment manufacturers to perfect their pump systems and achieve superior, long-lasting performance. They developed a guide to help various commercial industries, including the dust suppression industry, better understand how to achieve proper GPM and PSI, so check it out below.
Then, connect with the Pump experts at Pumptec for a no-obligation consultation to explore how their state-of-the-art technologies and decades of fluid control engineering experience can help you.