Soft Wash Spotlight: Preventative Maintenance of Pumps

Shawn Glover, VP of Sales, Jun 20, 2023
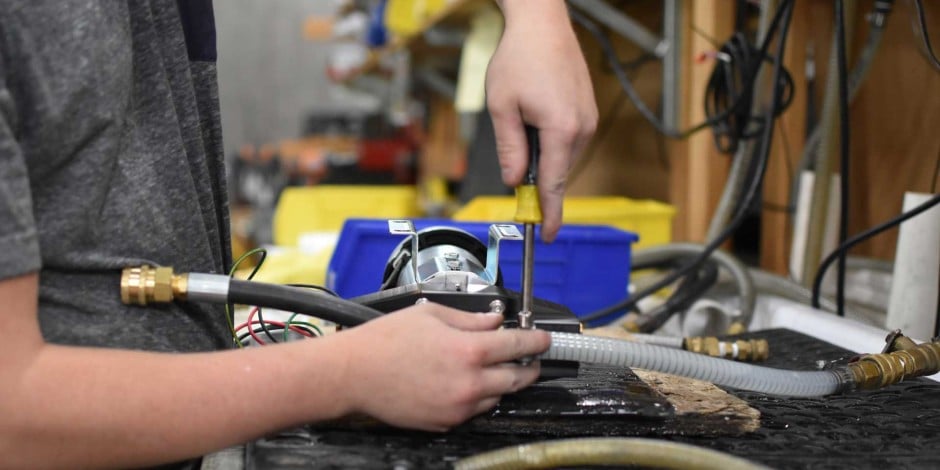
A soft wash machine is the key to an operator’s success, and the pump is arguably the heart of the machine and typically the most costly component. Preventative maintenance of the pump is critical to protect an operator’s investment and livelihood.
Pump maintenance isn’t always the same across the board, however. That’s because equipment manufacturers may configure different pump model options into a system to address various goals, performance requirements, or price points.
The two most common types of pumps used in soft wash systems are plunger pumps and diaphragm pumps. To understand the maintenance requirements first requires an understanding of the difference between the two.
The Difference Between Diaphragm vs. Plunger Pumps
Diaphragm pumps and plunger pumps are both positive displacement pumps and have some similarities. Both, for example, have reciprocating components. The diaphragm pump, however, has a diaphragm that flexes back and forth; the plunger pump’s mechanism is more rigid.
These variances make a big difference in the pump’s longevity. The flexible diaphragm has a tendency to rupture prematurely, while plunger pumps are engineered to withstand repeated high-pressure use over time.
One of the biggest differences often comes down to their power sources. To achieve enough pressure for commercial soft wash applications, diaphragm pumps typically need a gas engine. Because plunger pumps run much more efficiently, they have the option to operate using power from a vehicle’s battery while still maintaining optimal pump pressure (150 PSI) and flow (7 GPM). This allows for much quieter operation in residential areas, a smaller footprint, and fewer emissions.
In light of recent legislation banning gas-powered small off-road engines (SORE) in some states, electric plunger pumps are increasingly more desirable.
Another major difference between the two involves their maintenance. In a nutshell, a gas-powered unit will require more maintenance and labor than an electric plunger pump unit. And, while opting for a diaphragm pump in a soft wash system may have a lower price tag up front, the fuel, labor, operational costs, and total cost of ownership over time will most likely exceed that of a plunger pump investment. In the end, a diaphragm pump will need replacement much sooner than a quality plunger pump.
TAKE A DEEP DIVE: Plunger vs. Diaphragm Pump: How to Choose the Best Pump
Soft Wash Pump Preventative Maintenance Tips
The abrasive chemicals used in soft wash applications include sodium hypochlorite (bleach) and surfactants. These chemicals are typically mixed with water in a 55 gallon drum or a larger reservoir that is kept on the back of a truck bed or trailer. Precautions must be taken to ensure these chemicals do not corrode pump components.
The following preventative maintenance tips can mitigate the risks of pump failure and help maximize a pump’s lifespan.
RELATED CASE STUDY: Designing a Soft Wash System That Lasts
1. Flush the Pump System Daily
While soft wash systems are engineered to withstand corrosive compounds, those chemicals should not be left standing in the system. When not in use, chemicals should be drained into an appropriate container, then rinsed from the pump and hoses using fresh water. Operators who fail to properly flush and rinse their systems according to the manufacturer’s recommendations could void their warranty.
2. Consider Using Neutralizers
The use of a bleach neutralizer can help reduce the damaging effects of sodium hypochlorite. It can be used as a final rinse on cleaned surfaces and can also be used to rinse the inside of the soft wash system itself.
3. Clean Filters, Nozzles & Accessories
Consult your pump manufacturer’s manual to determine the proper cycle for cleaning various components.
- Check nozzles, spray guns, fittings, quick connects, and any visible components for scale buildup, and remove as needed
- Wipe down exposed surfaces with a damp cloth to remove any overspray of chemicals that could corrode materials
4. Inspect All Components
Get in the routine of inspecting your pump equipment daily to fend off potential issues.
- Inspect hoses for any wear, cuts, or holes
- Ensure that all mounting points and fittings are tight and properly sealed, as vibration could loosen fittings over time
- Check all electrical connections to ensure that wiring is secure and that there are no abrasions or exposed wires
- Likewise, inspect pressure gauges and regulators
Gas-powered units typically require additional maintenance and inspections for oil levels, fuel lines, and other components. Follow the pump manufacturer’s maintenance schedule for tasks such as oil and spark plug changes, leak detection, and filter cleaning and replacements.
GET OUR COMPLETE MAINTENANCE CHECKLIST! Download Now
5. Protect For Long-Term Storage
When not using a pump system for prolonged periods of time, be sure to follow proper storage protocols.
- Disconnect the battery
- Protect wiring to prevent rodent damage
- Consider flushing the system with RV antifreeze if kept in cold climates
- Store the pump system in a dry location
RELATED: Tips for Winterizing a Power Washer
Choosing a Soft Wash Pump System
In addition to proper maintenance, one of the best ways to ensure years of worry-free operation is to invest in the right pump in the first place. Pumptec plunger pumps are simply the best soft wash pumps available on the market, delivering consistent flow at ample pressure.
In particular, our XPVC pump is engineered for the soft wash industry and is the only A-rated system of its kind in the market. The pump body is constructed of PVC and CPVC and includes ceramic plungers, C276 alloy check valves, Viton o-rings, and other highly durable components. With proper maintenance, operators could double or triple the longevity of their system by opting for a plunger pump.
When looking for a durable pump to configure into your soft wash system, contact the Pumptec engineering team. We’ll talk through your needs and challenges and customize a solution to fit your application.
Also be sure to download our extensive pump maintenance checklist below.