Triplex Oil Bath vs. Sealed Bearing Pumps

Shawn Glover, VP of Sales, Mar 22, 2022
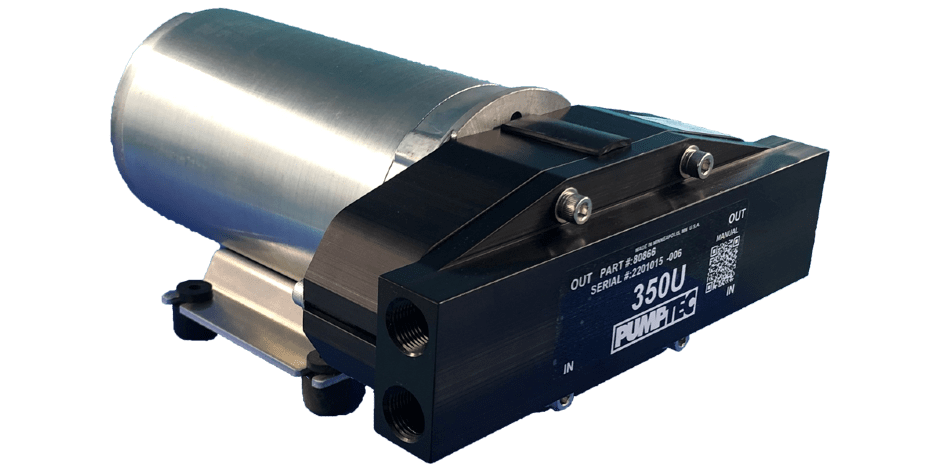
There is often a debate over whether triplex oil bath pumps or sealed bearing pumps are better. The truth is, there is a time and place for each, and the type of application and performance a pump operator requires will help them determine which is best.
Here, we’ll cover the difference between triplex oil bath and sealed bearing pumps, their pros and cons, and examples of where each may be suited.
How an Oil Bath Pump Works
An oil bath pump, commonly called a triplex plunger pump, is a three-cylinder pump that is driven by a crankshaft or wobble plate. The reservoir where the oil is contained is called a sump and must be filled and replenished manually. Oil splashes onto the crankshaft and connecting rods that drive the plungers in and out, providing lubrication. For proper operation, an oil bath pump should remain in a fixed position to eliminate the possibility of oil leaks and improper lubrication.
How a Sealed Bearing Pump Works
A sealed bearing pump has oil or grease contained in a sealed chamber which lubricates the ball bearings that drive the plunger in and out. The oil reservoir cannot be accessed and does not require replenishing or replacing. Since the grease is self-contained, it will not ooze out or leak when set on its side.
The mechanics and configuration of each type of pump differ considerably. To help distinguish proper selection, it’s important to understand how each performs and their pros and cons in the following areas.
Horsepower and Efficiency
Lower horsepower (HP) pump motors, like those used for chemical metering, commercial cleaning, misting, hydrostatic testing, and similar scale commercial applications need to be as efficient as possible. In these instances, sealed ball bearings waste less energy. This is especially important for electric and battery-powered units.
The transfer of rotational energy into the linear movement of a pump shaft naturally loses energy during operation. You want to minimize that effect as much as possible, especially at lower horsepowers. Consider a motor rated at 1.5 HP that runs at only 80% efficiency, which isn’t unheard of for oil bath pumps. Such a loss of power is unacceptable. Sealed ball bearings are much more efficient (as high as 93% efficiency), making them suitable for low horsepower applications.
Physics demands that at a certain point, however, you need to deploy a higher-powered pump. Industrial applications that require high flow rates and more horsepower typically require oil-bath pumps. Losing 15-20% horsepower during operation may be acceptable in a 50 HP motor as long as it still produces enough GPM and PSI.
Both types of pumps may be used in the same application but for different purposes. For example, triplex oil bath pumps may be used in a high-powered spray gun at a car wash. This function doesn’t require precise coverage or flow. The sealed bearing pump, however, would be ideal for injecting solvents into the car wash lines. Because of its configuration and size, it can be calibrated to dispense precise amounts of chemicals to properly wash vehicles.
Portability and Handling
For pump operators who haul their equipment in and out of job sites, a sealed bearing pump with encased grease has many advantages. Transporting oil bath pumps and maneuvering them on and off a truck bed, for example, has the potential to cause leaks. If not kept upright, an oil bath pump will drain out, leading to low oil levels and premature wear and eventual pump failure.
Sealed bearing pumps can run in any orientation and even be mounted upside down or stored on their sides. Because they don’t have a crankshaft, they are also much lighter and easily maneuverable.
Maintenance
The design of an oil bath pump is more complex than a sealed bearing pump, and the more moving parts you have, the more maintenance is required. The oil in an oil bath pump must be periodically drained and replaced according to the manufacturer’s maintenance schedule. High horsepower applications often use internal combustion gas engines which have maintenance issues of their own and can produce excessive vibration. This vibration can loosen drain plugs over time and result in an oil leak, stressing the importance of routine inspections. If the oil level in an oil bath pump is too high or too low, it will generate excessive heat which will degrade the oil and shorten the lifespan of the pump.
In general, sealed bearing pumps have a relatively simple design and require much less maintenance. Because the bearings are sealed, oil or grease levels do not require replenishing or replacing. Since there are fewer parts, there’s typically less that can go wrong.
RELATED: Get the Pump Maintenance Checklist
Overall Cost
Because oil bath pumps are more complex and have more moving parts, they will inevitably be more expensive than a sealed bearing pump. Total cost of ownership will also be more due to added labor, maintenance, and energy consumption over time.
When cost is a major consideration, it’s important to right-size your pump for your application. Bigger is not always better and may actually result in poor performance depending on your application. Take, for example, a soft wash pump application. A pump that produces too much flow and PSI will likely damage surfaces rather than clean them. Most soft wash applications are more suited to sealed bearing plunger pumps.
RELATED: Soft Wash Industry Pump Case Study
Customizability
The simpler design of sealed bearing plunger pumps makes them more customizable. In the case of Pumptec pumps, we use an offset cam which can be made in any size and makes it much more configurable. A direct drive pump design also makes switching out materials like PVC or aluminum easier.
Changing the displacement, materials, or diameter of a plunger on an oil bath pump takes a lot of engineering effort and requires machining of different crankshafts. Oil bath pump manufacturers typically try to limit the number of crankshafts used in their pump models to minimize costs. However, this means that pinpointing GPM and PSI for applications requiring precise output is limited.
In the end, it’s the application that will determine which pump is right for you. If you need excessive horsepower and flow, an oil bath pump may be appropriate. If your application requires precise flow and pressure, mobility, efficiency, and lower horsepower, a sealed bearing drive plunger pump will meet your needs.
At Pumptec, we specialize in commercial high-pressure pump designs featuring sealed bearings. Pumptec pumps are ideal for applications requiring up to 1200 PSI and up to 7 GPM and can be configured to most any specification. Speak with one of our pump experts today to help determine which pump design and output is best for your industry application. Also download our pump maintenance checklist below with additional considerations.