What You Need to Know About Hydrostatic Testing Pumps

Shawn Glover, VP of Sales, Jan 11, 2022
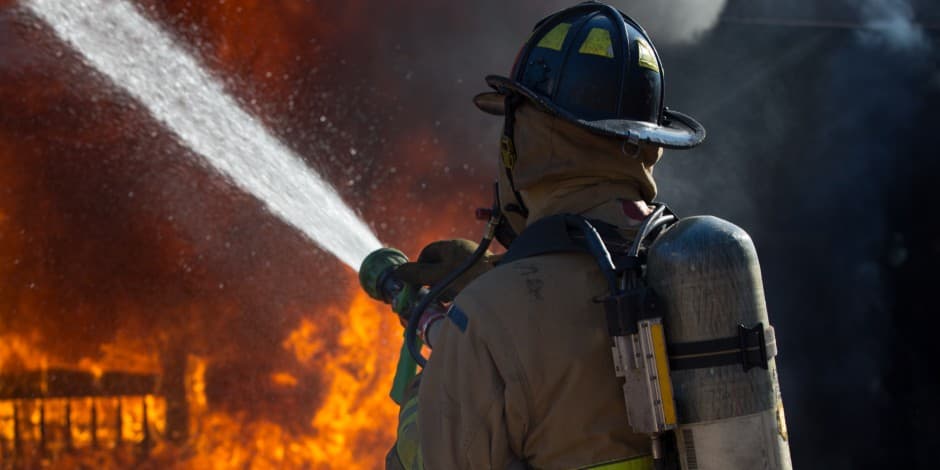
Hydrostatic testing is a critical process for many industries and applications that use equipment subjected to high pressure. In the end, however, a hydrostatic pressure test is only as good as the pump used to perform it. In other words, not only should the system being tested be structurally sound and perform as it should, the pump testing it also needs to be just as reliable and maintain appropriate pressure levels.
In today’s article, we’ll explain how hydrostatic testing works, common applications, and what to look for when choosing the best hydrostatic testing pump.
What is Hydrostatic Testing?
Hydrostatic testing (also referred to as hydro testing) is a type of test that fills a pressure vessel or pipe system with fluid to a specified PSI to ensure it can safely hold the amount of pressure it is rated for and maintain structural integrity. The item being tested must maintain its PSI for a designated period of time without leaking or rupturing. The length of time and PSI rating for each application’s hydrostatic test is typically determined by the manufacturer or government agency regulations.
A closed loop system must be created to perform a hydrostatic test which, in most cases, involves shutting off a supply valve. Most commonly, the pressurized fluid is water (from the Greek word hydro), and it is sometimes dyed to aid in visual inspection of leaks. Hydrostatic tests are often necessary after equipment shutdowns, repairs, or prolonged time sitting idle to verify that it will operate properly when it returns to service.
Common Hydrostatic Testing Applications
In theory, any system that needs to maintain pressure greater than the ambient pressure has the potential to benefit from a hydrostatic test. The following industries and applications are the most common examples of hydrostatic testing:
Sprinkler systems. By code, many sprinkler systems need to be tested periodically to ensure that they can maintain pressure when activated and operate properly. A pump is hooked up to the main sprinkler system line and pressurized to 250 PSI, which it needs to maintain for at least 15 minutes.
Fire hoses. Critical applications like fire hoses need to be tested to ensure they don’t rupture or fail in service. They are typically tested prior to being installed in fire trucks or brought to fire stations. Inspectors will flood hoses with fluid and pressurize it to a minimum of 300 PSI, in accordance with National Fire Protection Association (NFPA) specifications.
Pipe manufacturers. Commercial pipe manufacturing plants will perform hydrostatic testing on pipes of varying lengths, especially those supplied to government agencies. They need to prove that every pipe meets specifications and that they won’t experience failure in critical applications like naval defense vessels.
Cooling systems. Cylinders or coils for A/C or refrigeration units are routinely tested, particularly in facilities where climate control is critical like hospitals. Industrial electrical enclosures also use these types of refrigerants to cool down electronics, as do military vehicles used in extremely hot climates. Municipal vehicles like city buses also utilize cooling systems, and some state Department of Transportation agencies may require periodic testing to ensure safety and proper operation.
Miscellaneous. There are numerous other applications where hydrostatic testing is conducted, including oil and gas pipelines, irrigation systems, gas cylinders, boilers, sewer water lines, plumbing, and more.
What to Look for in a Hydrostatic Testing Pump
As you can see, a hydrostatic testing company might provide services to multiple industries. As such, it will require the use of a pump that can operate at different pressures that meet the desired specifications.
For example, a company might test fire sprinklers one day and fire hoses or plumbing systems the next. An operator could use a pump rated up to 1,200 PSI for when an application calls for it, and then turn it down to 250 PSI for a sprinkler test. The pump’s pressure is adjusted with the use of a pressure regulator to achieve that threshold. In the sprinkler test example, as soon as the pressure hits 250 PSI, it will bypass any additional pressure to maintain levels in the line.
Maintaining consistent pressure, however, is where the real value comes in. A hydrostatic test cannot have fluctuating pressure, which is what makes an electric plunger pump ideal. Unlike a diaphragm pump with flexible components, a plunger pump’s pressure will not ebb and flow. Both are considered positive displacement pumps, but have distinct differences.
Operators are also concerned with the amount of flow output that a pump can deliver. They don’t want to be standing around all day waiting for a system to fill and reach the desired PSI. The higher the flow rate of a pump, the faster the system will fill.
For many applications like fire hoses and sprinkler systems, you typically don’t want any less than 3.0 GPM. When used with a pressure gauge and regulator, our 350U and 356U series pumps have a lot of varying flow potential. When operating around 250 PSI, they can achieve a tremendous amount of flow and fill lines quicker so operators can get in and out of jobs faster, saving on labor costs.
Electric plunger pumps are not only ideal for their quiet operation and consistent flow and pressure, they’re also compact, portable, and easily maneuvered to fit into tight spaces.
Failure isn’t an option in critical systems or the hydrostatic testing pumps used to test them. Learn more about what sets Pumptec hydrostatic testing pumps apart from the competition, and how our engineers can customize a solution to your precise specifications. Speak with a pump expert today.
To learn more about plunger pumps and how they compare to other types of pumps, download our Pump Comparison Cheat Sheet below.