5 Factors Impacting High-Pressure Plunger Pump Prices

Shawn Glover, VP of Sales, Jan 3, 2023
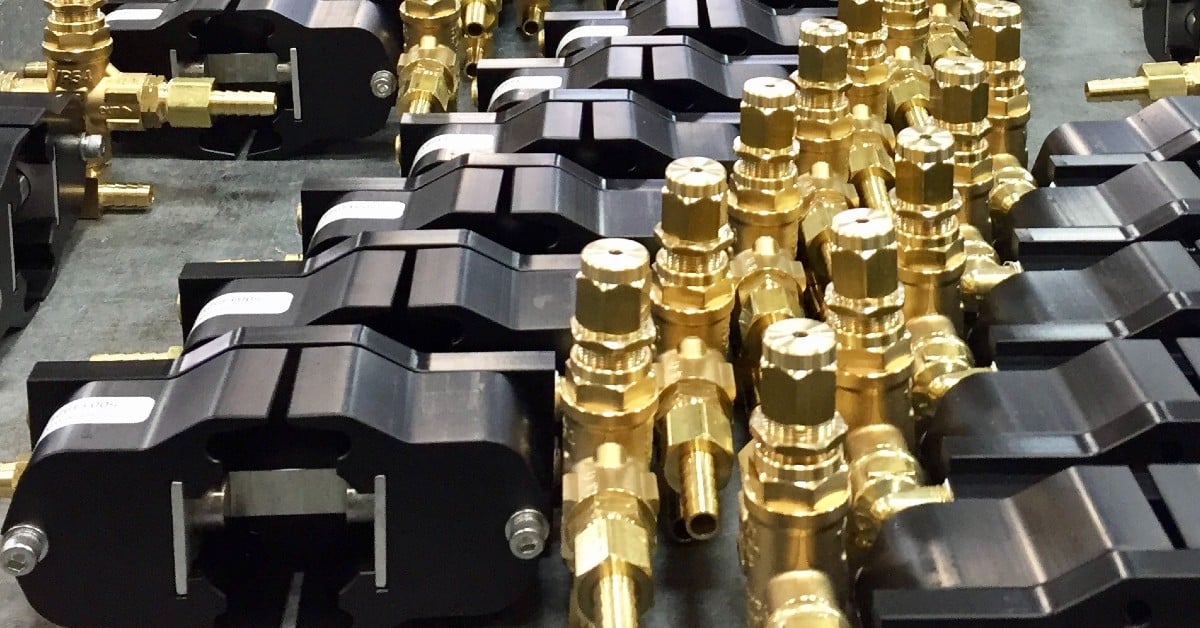
How much do Pumptec plunger pumps cost? It’s a fair question, and it’s one that we get asked a lot during initial conversations with customers. There are many factors that determine a high-pressure plunger pump price, and we often encourage users and equipment manufacturers to consider the total cost of ownership (TCO) vs. up-front costs.
That’s because the initial purchase price of a piece of equipment represents only a small fraction of its TCO. The collective costs of maintenance, repair fees, energy usage, warranty returns, downtime, and related labor could be ten times as much as the initial price tag.
Reducing pump costs over time is the ultimate goal.
Commercial industries that rely on pump equipment to get the job done need to know they’re receiving a good overall value. As you consider the following cost factors, think about the longevity of your commercial pump and its total cost of ownership.
1. Pump Materials
The materials that go into manufacturing a high-pressure pump play the biggest role in determining price. An entry-level residential diaphragm pump, for example, is typically made out of polycarbonate or plastic. While inexpensive, it’s not uncommon for a pump to only last a few months with repeated use, needing replacement the following season. Plastic often becomes brittle or compromised when exposed to UV rays, temperature fluctuations, harsh chemicals, and high pressure.
The best materials for industrial-grade commercial pumps are typically anodized aluminum or stainless steel. Despite costing more to manufacture up front, these materials are far more durable under high pressure, withstand harsh chemicals, and can last for many years. Less durable materials will never give you the performance and power you’re looking for.
Highly durable ceramic plungers may also be used and are more expensive than stainless steel. Ceramic should be considered for applications that need to withstand high temperatures, as it does not transfer heat like stainless steel does. This is an important factor in prolonging the life of your pump’s elastomers and seals, especially in low-volume, high-pressure applications like misting systems where temperatures can climb quickly. Excessive heat can degrade Buna or Viton elastomers and lead to eventual pump failure.
2. Custom vs. Off-the-Shelf Pump
What will end up costing more — an off-the-shelf pump or a custom-designed pump to fit into your existing equipment? It’s easy to reason that the ready-made pump will be cheaper, but deeper exploration often reveals a completely different story.
This is demonstrated in a customer’s experience with a pump for their insecticide and fertilizer spray rigs. The pump they used from another manufacturer was being discontinued. To determine whether we could fill the need, we asked exploratory questions about the required flow rate, pressure, and nozzle size. Turns out that, for years, the other manufacturer sold them a much larger (and more costly) off-the-shelf pump than they needed.
By customizing a right-sized solution, they ended up with a pump that was half the size and one-third the price. The costs and headaches of dealing with inferior pumps can quickly erode profits and patience.
RELATED ARTICLE: 6 Questions During the Custom Pump Design Process
3. Pump Design and Assembly
Some pump designs are more complex than others, bringing costs up. Within the plunger pump industry, you’ll typically find sealed bearing plunger or piston pumps and triplex plunger pumps. Triplex oil bath pump designs have a lot of moving parts and require significantly more maintenance than sealed bearing plunger pumps, making their up-front and total cost of ownership much higher.
While each has its place, commercial applications that require mobility are more suited to sealed bearing pumps, like those offered by Pumptec. Sealed bearing pumps can be tipped on their sides and are more conducive to being hauled on and off a truck whereas oil bath pumps will leak lubricant if not kept upright. The fact that sealed bearing pumps are almost always less expensive is a bonus.
Something to consider as part of the design process is whether to buy a standalone pump vs. a pump assembly. When you step into the commercial pump world, it’s not as simple as hooking up a couple hoses and going to work. A pump assembly is complete with the right hoses, fittings, accessories, and plumbing configurations to ensure it operates properly on day one and for years to come.
A plug-and-play custom assembly solution is arguably a far greater value over time.
4. Labor and Fittings
Those who are enticed by the lower price point of ready-made pumps often overlook many of the ancillary costs associated with configuring it into a system, making the pump assembly an appealing and value-driven choice.
It’s important to get answers to the following questions:
- Will the pump need to be modified to fit into my system?
- Is the pump a complete system that’s already plumbed or is it bare bones?
- Are the proper hoses, fittings, regulators, and other components included?
- Is it compatible with the fluids and chemicals I use?
- Will the pump provide the right power and flow rate for my application?
- Am I able to test the pump prior to purchasing it to make sure it meets specifications and operates as it should?
- What will the labor costs be to install it in my system and maintain it over time?
RELATED INFOGRAPHIC: How to Configure a Pump Into Your System
A pump assembly that’s custom fit for your equipment might cost more up front, but the labor to install it will decrease significantly because you won’t have to reconfigure anything. If you need a compact pump assembly for a commercial pressure cleaning sprayer that delivers 6 GPM at 300 PSI, a custom pump manufacturer will design a plug-and-play system to those exact specifications.
5. Engineering Support
Many OEMs have design or mechanical engineers on staff to design their commercial equipment. When that equipment requires a high-pressure pump, however, it’s critical to leverage the expertise of an engineer with deep knowledge of fluid control dynamics and who specializes in designing electric motor pump systems. Their skillset helps obtain peak performance and long-lasting durability through proper plumbing, configurations, flow rates, PSI, material selection, and more.
Most manufacturers don’t have a pump expert on staff, and a lot of time and money can be tied up in designing a system that may not be optimized for your needs. One of our greatest strengths at Pumptec is our team of pump experts and engineers who design a system to meet a specific goal: yours. We serve as an extension of your team, collaborating with your engineers at no cost, building prototypes, testing, and more.
Speak with a pump expert today to see how a custom pump solution can truly provide greater lifetime value.